When it comes to renovating your kitchen, the floor is an often overlooked aspect. Many people simply choose to go with whatever is cheapest or easiest. But when you put in a little extra effort, you can create a beautiful and unique floor that will really stand out.
There are many different hardwood flooring options available on the market today. You can choose from a variety of colors, textures, and finishes. But with so many choices, it can be difficult to know where to start. That’s why we’ve put together this guide to help you choose the best hardwood floors for your kitchen.
Engineered or Solid Hardwood Floors
One of the first decisions you’ll need to make is whether to go with engineered or solid hardwood floors. Engineered hardwood floors are made up of a core of plywood or HDF, topped with a thin layer of hardwood veneer. Solid hardwood floors are exactly what they sound like – they’re made entirely of solid wood.
There are a few things you’ll need to consider when making this decision. First, engineered hardwood floors are more stable than solid hardwood floors. This means that they’re less likely to warp or cup over time. If you live in an area with high humidity, this can be a big advantage.
Second, engineered hardwood floors are often thinner than solid hardwood floors. This can be a good thing or a bad thing, depending on your needs. If you’re looking to install the flooring over an existing floor, thinner floors may be a better option. However, if you want your floors to have a more substantial look and feel, you may prefer solid hardwood floors.
Finally, engineered hardwood floors are typically more expensive than solid hardwood floors. If cost is a major consideration for you, solid hardwood floors may be the better option.
What Type of Finish Should You Choose?
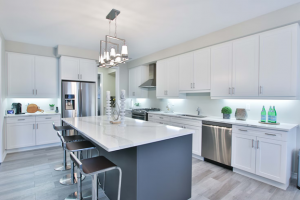
Source: Unsplash
Once you’ve decided on engineered or solid hardwood floors, the next step is to choose a finish.
The type of finish you choose will have a big impact on the overall look and feel of your floors. It’s important to take some time to think about the style you’re going for before making a decision.
Because a kitchen’s hardwood flooring has above-average exposure to frequent use and abuse, the finish you pick is particularly vital. Since there’s a high chance water will get on the floor, your finish has to be waterproof. It also must be strong enough to endure the heavy foot activity that a kitchen receives.
Oil-Based Finish
One popular option is an oil-based finish. Oil-based finishes give hardwood floors a natural, warm appearance. They’re also easy to touch up and repair if they get scratched or damaged. Another advantage of oil-based finishes is that they’re very durable. They can withstand a lot of wear and tear, making them a good choice for high-traffic areas.
Water-Based Finishes
Another popular option is a water-based finish. Water-based finishes provide a harder, more durable surface. However, they can be more difficult to touch up and repair than oil-based finishes. Water-based finishes are also easier to apply than oil-based finishes and are less likely to yellow over time.
Wax Finish
If you’re looking for an old-fashioned look, you might consider a wax finish. Wax finishes are easy to apply and provide a beautiful, natural sheen. However, they require more maintenance than other types of finishes and can be difficult to repair if damaged. Wax finishes are also more susceptible to scratches and scuffs.
Polyurethane Finish
For a high-gloss, durable finish, you might want to choose a polyurethane finish. Polyurethane finishes are more resistant to scratches and stains than other types of finishes. However, they can be more difficult to apply and may yellow over time.
Moisture-Cure Urethane
If you’re looking for a finish that’s extremely durable and resistant to moisture, you might want to choose a moisture-cure urethane. Moisture-cure urethanes are more difficult to apply than other types of finishes. They also have a strong odor and can be dangerous if used improperly.
Shellac
Shellac is a type of finish that’s made from lacquer. It’s easy to apply and dries quickly. However, it’s not as durable as other types of finishes and can be difficult to repair if it’s damaged. Shellac is also more susceptible to scratches and scuffs.
Penetrating Oil Sealer
A penetrating oil sealer is a good choice if you want to protect your floors from water damage. Penetrating oil sealers soak into the wood, creating a barrier that prevents water from damaging the floors. However, penetrating oil sealers don’t provide as much protection from scratches and scuffs as other types of finishes.
Acid-Cured Finish
An acid-cured finish is a good choice if you’re looking for a durable, high-gloss finish. Acid-cured finishes are more difficult to apply than other types of finishes. They also have a strong odor and can be dangerous if used improperly, as well as being more susceptible to scratches and scuffs.
Prefinished Flooring
Prefinished flooring is a great option if you want to avoid the hassle of applying a finish to your floors. Prefinished flooring comes with a factory-applied finish that’s already dried and cured. Prefinished flooring can be a bit pricier, however you save time and money with flooring that is already finished. This option allows you to enjoy your new floors immediately.
Which Type of Flooring is Best for Your Kitchen?
Now that you know a little bit more about the different types of hardwood floors available, it’s time to decide which one is right for your kitchen.
If you’re looking for a durable, easy-to-maintain floor, engineered hardwood or a water-based finish might be the best option for you. If you’re looking for a more traditional look, solid hardwood or a wax finish might be the way to go. And if you’re looking for a high-gloss, durable finish, polyurethane might be the right choice. If you’d like to be able to enjoy your floors immediately without the hassle of applying a finish, prefinished flooring is your best option. It all depends on what you’re looking for in your kitchen’s flooring.
Chances are, you probably don’t know exactly what you want yet. The best thing you can do in this situation is to contact our team for a custom, free consultation. We would love to help you.
Should You DIY or Hire a Professional?
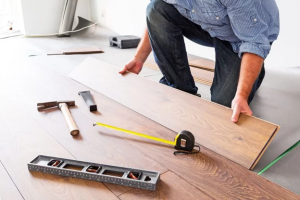
Source: Unsplash
Once you’ve decided on the type of hardwood floors you want, you’ll need to decide whether to install them yourself or hire a professional. If you’re handy and have some experience with home improvement projects, installing hardwood floors yourself can be a great way to save money.
However, hardwood floors can be tricky to install. If you’re not confident in your ability to do it yourself, hiring a professional is your best option. Not only will they be able to get the job done quickly and efficiently, but they’ll also be able to offer advice and guidance if you run into any problems.
Final Thoughts
When it comes to choosing the best hardwood flooring for your kitchen, there are a lot of factors to consider. But with so many great options available, you’re sure to find the perfect floors for your home. Just take your time, do your research, and pick what works best for your unique needs.
Now that you know more about the different types of hardwood floors available, you can start planning your kitchen renovation. With a little bit of research and planning, you can create the perfect space for cooking, entertaining, and spending time with family and friends. So what are you waiting for? Get started today!